What is a CMMS?
27 May 2024 – Reading time : 5 min – Wrote by François GRANDHAY
What is a CMMS? What you need to know
A Computerized Maintenance Management System (CMMS) is a software tool designed to streamline maintenance operations, manage assets, and improve efficiency. But what is a CMMS in detail? It automates tasks such as work order management, preventive maintenance scheduling, and inventory control.
By providing real-time data and analytics, a CMMS helps organizations reduce downtime, extend asset lifespan, and ensure regulatory compliance. Understanding what is a CMMS is essential for businesses looking to enhance their maintenance strategies and achieve operational excellence.
__________________
Introduction to CMMS
Definition of CMMS
CMMS software provides a centralized platform where maintenance teams can create, manage, and track work orders, schedule preventive maintenance tasks, and monitor equipment performance. This ensures that all maintenance activities are carried out efficiently and effectively.
- Work Order Management: Create, assign, and track maintenance tasks.
- Preventive Maintenance: Schedule regular maintenance to prevent equipment failures.
- Asset Management: Monitor and manage the lifecycle of assets.
- Inventory Management: Track and manage spare parts and supplies.
- Reporting and Analytics: Generate reports to analyze maintenance performance.
By integrating a CMMS into their operations, organizations can achieve better maintenance efficiency, reduce costs, and improve overall asset management. Understanding the definition and capabilities of a CMMS is the first step towards optimizing your maintenance strategy.
History of CMMS
In the 1980s, the advent of personal computers and more user-friendly software led to the development of more sophisticated CMMS solutions. This period saw the transition from manual maintenance tracking methods to automated systems, significantly improving maintenance efficiency.
During the 1990s and 2000s, CMMS software evolved further with the integration of more advanced features such as work order management, preventive maintenance scheduling, and asset tracking. The introduction of web-based CMMS solutions allowed for easier access and collaboration among maintenance teams.
Today, modern CMMS platforms, like Bob! Desk, offer comprehensive solutions that incorporate mobile capabilities, real-time data analytics, and integration with other enterprise systems. These advancements have made CMMS an essential tool for organizations looking to optimize their maintenance operations and achieve better asset management.
- 1960s: Early computer systems for maintenance management.
- 1980s: Personal computers and user-friendly CMMS software.
- 1990s-2000s: Web-based solutions and advanced features.
- Today: Modern, integrated, and mobile-friendly CMMS platforms.
Understanding the history of CMMS helps appreciate its evolution and the significant impact it has on modern maintenance practices.
How CMMS Works
The key components of a CMMS include:
- Asset Database: A comprehensive inventory of all equipment and assets, including their specifications, location, and maintenance history.
- Work Order Management: The ability to create, assign, and track work orders for maintenance tasks. This ensures that all tasks are completed efficiently and on time.
- Preventive Maintenance Scheduling: Automated scheduling of regular maintenance tasks to prevent unexpected equipment failures and reduce downtime.
- Inventory Management: Tracking and managing spare parts and supplies to ensure that necessary items are always available for maintenance tasks.
- Reporting and Analytics: Generating detailed reports and analytics to monitor maintenance performance, identify trends, and make data-driven decisions.
- Mobile Access: Enabling maintenance teams to access the CMMS via mobile devices, ensuring real-time updates and communication.
By integrating these components, a CMMS like Bob! Desk streamlines maintenance operations, reduces downtime, and enhances overall efficiency. This leads to significant cost savings and improved asset management for organizations.
Importance of CMMS in Modern Maintenance
A CMMS provides numerous benefits that are crucial for modern maintenance practices:
- Enhanced Efficiency: Automates routine tasks, reducing manual work and human error.
- Improved Asset Lifespan: Regular maintenance schedules help extend the life of equipment.
- Cost Reduction: Minimizes unexpected breakdowns and repair costs through preventive maintenance.
- Data-Driven Decisions: Provides valuable insights and analytics for better decision-making.
- Compliance and Safety: Ensures adherence to industry regulations and safety standards.
Implementing a CMMS like Bob! Desk allows organizations to optimize their maintenance operations, leading to significant cost savings, increased asset reliability, and overall operational excellence.
Key Features of CMMS
Work Order Management
Key benefits of work order management in a CMMS include:
- Centralized Task Management: All maintenance tasks are organized in one place, making it easy to prioritize and manage them.
- Automated Workflows: Automates the process of creating and assigning work orders, reducing manual intervention and errors.
- Real-Time Updates: Provides real-time updates on the status of work orders, ensuring transparency and accountability.
- Historical Data: Maintains a history of all work orders, which helps in analyzing past performance and planning future maintenance activities.
Using a CMMS like Bob! Desk for work order management ensures that maintenance operations are streamlined, efficient, and effective, ultimately leading to improved asset reliability and reduced downtime.
Preventive Maintenance
Key benefits of preventive maintenance include:
- Reduced Downtime: Regular maintenance helps prevent unexpected equipment breakdowns.
- Extended Equipment Lifespan: Consistent care and maintenance prolong the life of assets.
- Cost Savings: Preventing major repairs and replacements saves money in the long run.
- Improved Safety: Regular inspections help identify and mitigate potential safety hazards.
- Enhanced Efficiency: Well-maintained equipment operates more efficiently, leading to better performance.
Implementing a robust preventive maintenance program with a CMMS can significantly improve maintenance outcomes. For more detailed information on preventive maintenance, refer to this comprehensive guide.
Asset Management
Key benefits of asset management include:
- Comprehensive Asset Tracking: Keeps detailed records of all assets, including specifications, location, and maintenance history.
- Lifecycle Management: Monitors the entire lifecycle of assets, from acquisition to disposal.
- Maintenance Scheduling: Automatically schedules maintenance tasks to ensure assets are serviced regularly.
- Cost Management: Tracks maintenance costs and helps identify cost-saving opportunities.
- Improved Utilization: Ensures assets are used efficiently, reducing idle time and maximizing productivity.
Effective asset management is critical for organizations to maintain optimal operational efficiency and reduce costs. For further reading on asset management, check out this resource on asset management.
Inventory Management
Key benefits of inventory management include:
- Optimized Stock Levels: Maintains optimal levels of inventory to avoid overstocking or stockouts.
- Automated Reordering: Automatically generates purchase orders when stock levels fall below a certain threshold.
- Cost Control: Tracks inventory costs and helps identify opportunities for cost savings.
- Real-Time Tracking: Provides real-time visibility into inventory levels and locations.
- Improved Accuracy: Reduces errors in inventory management through automation and accurate record-keeping.
Implementing robust inventory management practices with a CMMS can greatly enhance maintenance efficiency and reduce operational costs. For more insights on inventory management, explore this comprehensive guide.
Reporting and Analytics
Key benefits of reporting and analytics include:
- Data-Driven Decisions: Provides actionable insights based on real-time data.
- Performance Tracking: Monitors key performance indicators (KPIs) to evaluate maintenance efficiency.
- Trend Analysis: Identifies patterns and trends in maintenance activities.
- Compliance Reporting: Generates reports to ensure compliance with industry regulations and standards.
- Customized Reports: Allows for the creation of tailored reports to meet specific organizational needs.
Utilizing advanced reporting and analytics features in a CMMS can significantly enhance maintenance operations and overall business performance. For more details on the importance of reporting and analytics, visit this resource on maintenance management.
Mobile CMMS
Key benefits of mobile CMMS include:
- Real-Time Access: Allows maintenance technicians to access work orders, asset information, and maintenance schedules in real-time from any location.
- Increased Productivity: Reduces the time spent traveling back to a central office to retrieve or update information.
- Instant Updates: Provides immediate updates on task status, ensuring better communication and coordination.
- Offline Capability: Enables work in areas without internet connectivity, syncing data once a connection is reestablished.
- Improved Accuracy: Reduces errors by allowing technicians to enter data directly into the system while performing maintenance tasks.
Implementing a mobile CMMS can greatly enhance the efficiency and effectiveness of maintenance operations. For more information on the benefits of mobile CMMS, refer to this resource on mobile CMMS.
Integrations and API Connections
Key advantages of integrations and API connections include:
- Data Synchronization: Ensures that data is consistent and up-to-date across all integrated systems.
- Enhanced Functionality: Combines the strengths of different software solutions, providing a more comprehensive toolset.
- Streamlined Operations: Reduces manual data entry and the risk of errors by automating data transfer between systems.
- Improved Reporting: Aggregates data from multiple sources for more accurate and insightful reporting.
For instance, a CMMS can integrate with Enterprise Resource Planning (ERP) systems, IoT devices, and other business applications, creating a more efficient and interconnected maintenance environment.
To explore more about the benefits and capabilities of CMMS integrations, visit this guide on CMMS integrations.
Regulatory Compliance
One of the primary ways a CMMS aids in compliance is through meticulous record-keeping. The system logs all maintenance actions, inspections, and repairs, providing a detailed audit trail that can be reviewed during regulatory inspections. This feature is particularly important for industries such as healthcare, pharmaceuticals, and manufacturing, where stringent compliance standards are in place.
Moreover, a CMMS can automate the scheduling of compliance-related tasks, ensuring that no inspections or maintenance activities are missed. This proactive approach helps prevent violations and the associated penalties, enhancing overall operational integrity.
An example of how a CMMS supports regulatory compliance is through its ability to generate compliance reports. These reports can be tailored to meet the specific requirements of various regulatory bodies, making it easier for organizations to demonstrate their adherence to regulations.
For more information on how a CMMS can assist with regulatory compliance, check out this detailed article on CMMS and compliance.
Predictive Maintenance
Unlike preventive maintenance, which is based on a fixed schedule, predictive maintenance uses real-time data and historical trends to optimize maintenance timing. Technologies such as IoT sensors, machine learning algorithms, and big data analytics play a crucial role in this process.
By implementing predictive maintenance, organizations can achieve:
- Reduced Unplanned Downtime: Address potential failures before they happen.
- Cost Efficiency: Minimize unnecessary maintenance activities and reduce repair costs.
- Extended Equipment Lifespan: Optimize maintenance schedules to enhance asset longevity.
- Enhanced Safety: Predict and mitigate risks associated with equipment failures.
For a deeper dive into predictive maintenance strategies and their benefits, visit this comprehensive guide on predictive maintenance.
Ready to simplify your maintenance management?
Découvrez la simplicité et l’efficacité de Bob! Desk dès aujourd’hui!
Benefits of Using a CMMS
Improved Efficiency
Key efficiency improvements include:
- Automated Scheduling: Ensures timely maintenance tasks without manual intervention.
- Real-Time Updates: Provides instant access to maintenance data and task statuses.
- Enhanced Communication: Improves coordination between maintenance teams and other departments.
For more insights on how a CMMS can improve efficiency, visit this article on CMMS efficiency.
Cost Savings
Cost-saving benefits include:
- Preventive Maintenance: Reduces the frequency and severity of equipment failures.
- Optimized Inventory Management: Lowers costs by maintaining optimal stock levels.
- Extended Asset Lifespan: Increases the useful life of equipment, delaying capital expenditures.
To explore more about the cost-saving potential of a CMMS, check out this guide on CMMS cost savings.
Regulatory Compliance
Benefits of regulatory compliance through a CMMS include:
- Detailed Record-Keeping: Maintains accurate records for audits and inspections.
- Automated Compliance Tasks: Schedules regular compliance-related maintenance activities.
- Audit Trail: Provides a comprehensive audit trail for regulatory review.
For more information, refer to this detailed guide on CMMS and compliance.
Enhanced Reporting
Advantages of enhanced reporting include:
- Customizable Reports: Tailor reports to meet specific organizational needs.
- Performance Monitoring: Track key performance indicators (KPIs) and metrics.
- Data Visualization: Use graphs and charts for easy data interpretation.
For a comprehensive overview, visit this guide on CMMS reporting.
Better Decision Making
Key decision-making benefits include:
- Data-Driven Insights: Utilize accurate data to guide maintenance strategies.
- Trend Analysis: Identify patterns and trends to optimize maintenance schedules.
- Predictive Analytics: Anticipate potential issues and plan accordingly.
Explore more on how a CMMS enhances decision making in this resource on CMMS and decision making.
Increased Asset Lifespan
A CMMS helps achieve this by:
- Regular Maintenance: Scheduling routine maintenance tasks to prevent wear and tear.
- Timely Repairs: Promptly addressing issues before they escalate into major problems.
- Condition Monitoring: Using real-time data to monitor asset health and predict potential failures.
By maintaining equipment in optimal condition, a CMMS reduces the need for frequent replacements and maximizes the return on investment for each asset. To learn more about how a CMMS can extend asset lifespan, check out this detailed guide on asset management.
Workflow Visibility
With a CMMS, organizations can:
- Track Work Orders: Monitor the status of work orders in real-time.
- Assign Tasks: Clearly assign responsibilities and ensure accountability.
- Monitor Progress: Gain insights into the progress of maintenance activities.
Enhanced workflow visibility helps in identifying bottlenecks and optimizing processes, leading to more efficient maintenance operations. For more information, visit this guide on workflow visibility in CMMS.
Safety and Health Improvement
Key aspects include:
- Routine Inspections: Regularly scheduled inspections to identify and mitigate potential hazards.
- Compliance Tracking: Ensuring adherence to safety regulations and standards.
- Incident Reporting: Facilitating quick reporting and resolution of safety incidents.
Using a CMMS to improve safety and health standards leads to fewer workplace accidents and a healthier work environment. To explore this topic further, check out this resource on CMMS and safety.
Automation of Processes
Key automated processes include:
- Work Order Generation: Automatically creates and assigns work orders based on predefined triggers.
- Preventive Maintenance Scheduling: Schedules regular maintenance tasks without manual input.
- Inventory Replenishment: Triggers automatic reorder of parts when stock levels are low.
Automation enhances efficiency and allows maintenance teams to focus on more strategic tasks. For more details, check this article on CMMS automation.
Mobile Workforce Enablement
Benefits include:
- Real-Time Data Access: Technicians can access and update work orders on the go.
- Increased Productivity: Reduces travel time to and from the office for updates.
- Instant Communication: Facilitates better communication among team members.
Enabling a mobile workforce ensures maintenance tasks are completed faster and more accurately. For more insights, visit this resource on mobile CMMS.
Implementing a CMMS
Choosing the Right CMMS
Consider the following:
- Functionality: Ensure the CMMS has all the features required for your maintenance operations.
- Scalability: Choose a system that can grow with your organization.
- User-Friendliness: The interface should be intuitive and easy for your team to use.
- Integration Capabilities: Ensure it can integrate with existing systems.
- Cost: Evaluate the total cost of ownership, including implementation and training costs.
Thoroughly researching and comparing different CMMS options will help you make an informed decision that aligns with your maintenance strategy. For more guidance, visit this guide on selecting a CMMS.
Steps for Successful Implementation
- Needs Assessment: Identify your organization’s maintenance needs and goals. This step involves gathering input from all stakeholders to ensure the CMMS will address all critical requirements.
- System Configuration: Customize the CMMS to fit your specific workflows and processes. This may include setting up user roles, permissions, and notification settings.
- Data Migration: Transfer existing maintenance data into the new system. Ensure data accuracy and completeness to avoid issues down the line.
- Training and Support: Provide comprehensive training to all users. Continuous support and resources should be available to address any questions or challenges that arise.
Following these steps will help ensure a smooth and successful CMMS implementation, leading to improved maintenance operations and efficiency. For a detailed implementation plan, refer to this CMMS implementation guide.
Needs Assessment
System Configuration
Data Migration
Training and Support
Challenges in CMMS Implementation
Common Obstacles
- Resistance to Change: Employees may resist adopting new technologies and workflows.
- Data Quality Issues: Inaccurate or incomplete data can hinder the effectiveness of the CMMS.
- Integration Difficulties: Ensuring the CMMS integrates seamlessly with existing systems can be complex.
- Training Gaps: Insufficient training can lead to underutilization of the system’s capabilities.
- Cost Concerns: The initial cost of implementation and ongoing maintenance can be significant.
Solutions and Best Practices
- Change Management: Implement a structured change management process to address resistance and ensure smooth adoption.
- Data Cleaning: Invest time in cleaning and organizing data before migration to ensure accuracy.
- Integration Planning: Work with IT specialists to plan and execute seamless integrations.
- Comprehensive Training: Provide extensive training and ongoing support to ensure all users are proficient in using the CMMS.
- Cost-Benefit Analysis: Conduct a thorough cost-benefit analysis to justify the investment and plan for future expenses.
Adopting these best practices can help mitigate the challenges of CMMS implementation and lead to a successful deployment. For more tips and strategies, refer to this guide on CMMS implementation best practices.
Future of CMMS
Technological Advancements
- Internet of Things (IoT): IoT sensors provide real-time data on equipment health, enabling predictive maintenance.
- Artificial Intelligence (AI): AI-driven analytics improve decision-making and optimize maintenance schedules.
- Augmented Reality (AR): AR assists technicians with real-time visual guidance for maintenance tasks.
These technological advancements are making CMMS more powerful and user-friendly, driving significant improvements in maintenance operations.
Trends to Watch
- Cloud-Based Solutions: Increasing adoption of cloud-based CMMS for greater accessibility and scalability.
- Mobile Integration: Enhanced mobile capabilities for on-the-go access and real-time updates.
- Sustainability Focus: Incorporating sustainability practices in maintenance to reduce environmental impact.
- Enhanced Cybersecurity: Strengthening cybersecurity measures to protect sensitive maintenance data.
By staying informed about these trends, organizations can leverage the latest innovations to optimize their maintenance strategies. For more insights, refer to this article on the future of CMMS.
Why Choose Bob! Desk?
Overview of Bob! Desk
With Bob! Desk, organizations can efficiently manage work orders, schedule preventive maintenance, and track asset performance. The platform is accessible on multiple devices, ensuring that maintenance teams can stay connected and productive from anywhere.
Unique Features of Bob! Desk
- User-Friendly Interface: Easy to navigate, reducing the learning curve for new users.
- Mobile Compatibility: Access the CMMS on smartphones and tablets for on-the-go updates.
- Customizable Dashboards: Tailor dashboards to display the most relevant information for your team.
- Advanced Analytics: Leverage data analytics to gain insights and optimize maintenance strategies.
- Seamless Integrations: Connect with other enterprise systems to enhance functionality and data flow.
These features make Bob! Desk an ideal choice for organizations looking to enhance their maintenance operations and improve asset management.
Benefits of Bob! Desk for Your Business
- Enhanced Efficiency: Streamlines maintenance tasks, reducing downtime and boosting productivity.
- Cost Savings: Optimizes maintenance schedules and inventory management, leading to significant cost reductions.
- Improved Asset Management: Extends the lifespan of assets through proactive maintenance strategies.
- Data-Driven Insights: Provides comprehensive analytics for informed decision-making.
- Regulatory Compliance: Ensures adherence to industry standards and regulations.
Choosing Bob! Desk means equipping your business with a powerful tool to drive operational excellence.
Customer Success Stories
- Retail Chain: Reduced maintenance costs by 30% and improved equipment uptime.
- Manufacturing Plant: Achieved a 25% increase in operational efficiency through predictive maintenance.
- Healthcare Facility: Enhanced compliance with regulatory standards, ensuring patient safety and equipment reliability.
These success stories highlight how Bob! Desk can deliver tangible results across various industries, driving growth and efficiency.
Key points from the article
Summary of Key Points
Final Thoughts
An expert team at your service
Choosing Bob! Desk and our CMMS software, you’re choosing a team based in Paris, available from 8am to 10pm, 6 days a week, to answer any questions you may have.
A passionate, responsive team that loves to toast its customers! 🍾
See you soon!
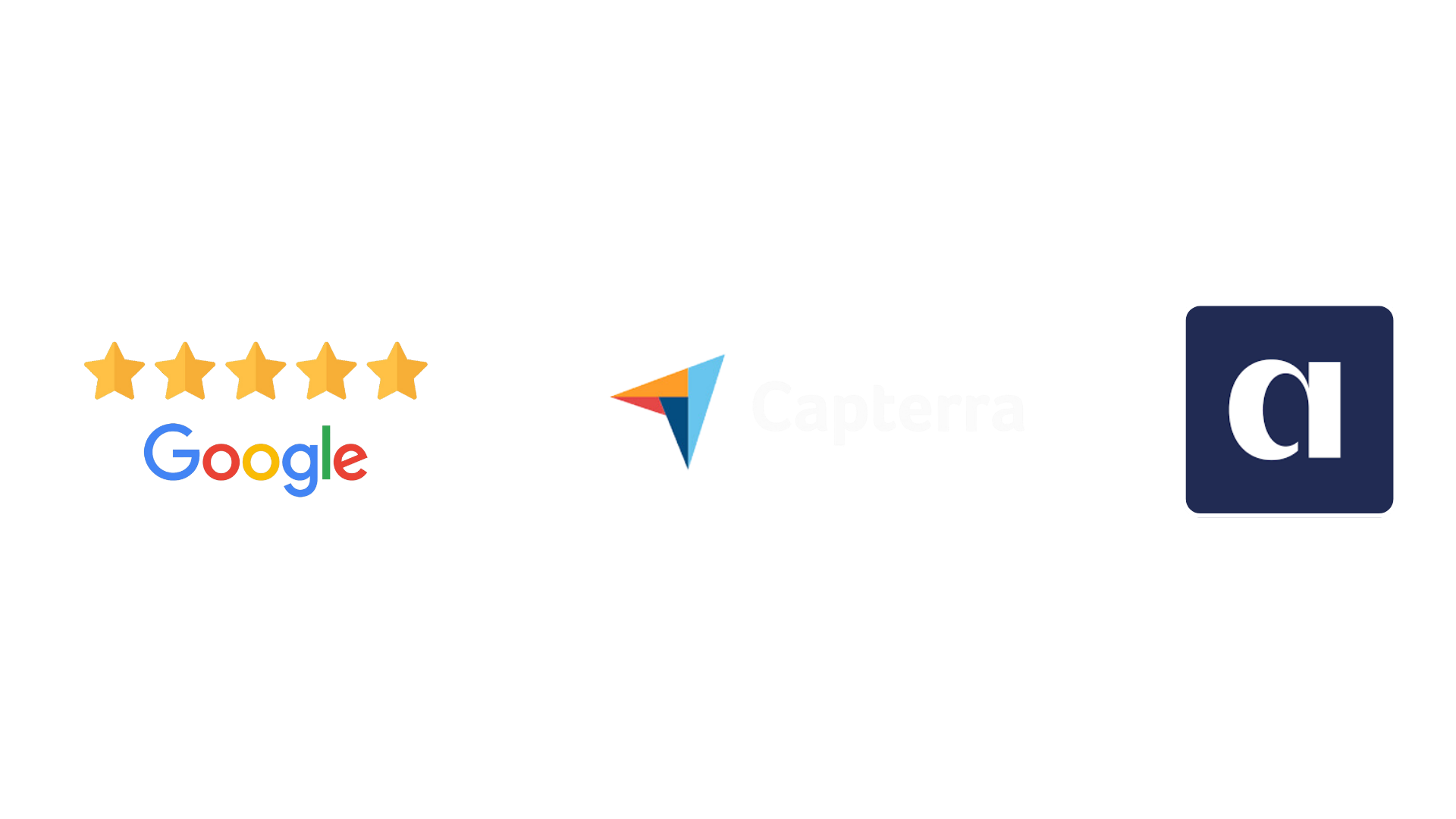